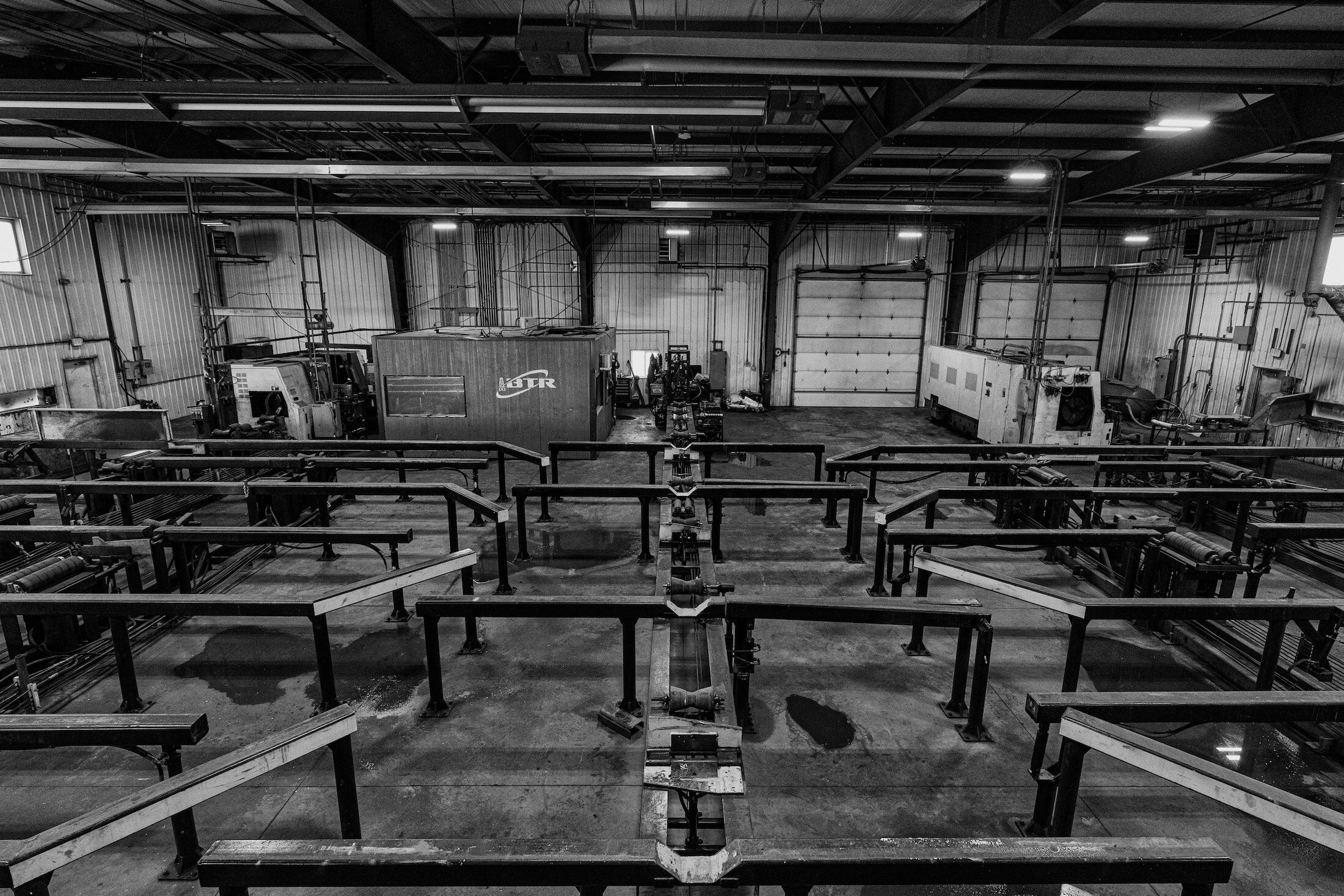
Contact Us
10285 3w Street SW
Killdeer, ND 58640
O: +1 (701) 764-7276
24 Hour Line; +1 (701) 495-2434
Scheduling and Pricing, please contact:
JobCoordinator@btrllc.com
Technical Questions, please contact:
OperationsManager@btrllc.com
Hours
M-F 6:00 A.M. - 4:00 P.M. MST
Sa Closed
Su Closed
BTR is a licensed API machine shop that can rethread various premium drill pipe, casing, and tubing connections.
Bakken Thread Repair was constructed to optimize efficiency. There is one incoming rack which feeds two working lines that four CNC lathes turn from. The shop’s layout, as well as our handling racks were all designed and fabricated in-house to suit our specific needs. The productivity we are able to achieve helps us meet customer deadlines with a high degree of quality.
BTR has more to offer than efficient machine work. We can handle our customer’s needs with bucking, hardbanding, inspection, straightening, and pipe storage.
Pipe Repair
Drill Pipe, Heavyweight, Drill Collars
API Connections
Various Premium Connections (see below)
Casing
Capabilities to cut up to 9.625”
Capabilities to buck up to 7”
Semi-premium (see below)
Tubing
API Connections
PH6
Pipe Straightening
Hardbanding
Duraband
Tuffband
Ultraband
Pipe Management
Storage
Inspection
Trucking

Bakken Thread Repair’s Quality Policy
At Bakken Thread Repair, our culture is one where quality is everyone’s responsibility and integral to everything we do. Our employees strive to improve our customer service in order to better satisfy the needs of all our clients through on time delivery, defect-free products, and cost-effective services. Our Owners/Managers make a daily commitment to this quality policy by demonstrating leadership that guides all employees in the continual improvement of our quality, service, value, and technology.
Our commitment to this Quality Management System guides BTR’s personnel to be ever mindful of the respective role each plays in the company for providing quality products and dedicated services.
The Goals of Bakken Thread Repair
Achieve total customer satisfaction by:
Producing quality products
Properly using quality documents
Delivering products on time
Conducting business communications promptly and professionally
Meeting all customer requirements
Meeting all statutory or regulatory requirements
Reach company’s full potential by:
Reaching maximum efficiency while achieving maximum quality
Setting the bar for customer relations
Establish and commit to quality processes through:
Measurement control
Quality checks
Quality audits
On the job training
Commit to continual improvement in all processes
The Owners/Managers of BTR have formulated and approved this quality policy This policy is implemented through employee orientation and training, as well as being posted in prominent locations within the company as a visual incentive for all employees.
Licenses
API Spec 5CT
BC
LC
SC
EU
NU
API Spec 7-1
API Numbered Connections
Full Hole
IF
X-Hole
REG
Proprietary Licenses
GB Connections
GB CD Buttress
Houston International Specialty, Inc
HIS-TCBC HT
Fermata Technologies, LLC ®
Rattler ®
Cobra ® SP
Bushmaster ® GT
Norris International
NTS-6
NTS-8
Frac String Solutions
FSS-247
FSS-265
Tejas Tubulars
TTWS
Spearhead
Texas Steel Conversions
TSDS-38
TSDS-42
Command Tubulars
CET-39
CET-43
Killdeer, North Dakota
Use the interactive map to find us